TKF in Lochem stellt Stromkabel mit einer Länge von bis zu 8 km her, die Windkraftanlagen im Meer miteinander verbinden. Der Produktionsprozess muss von Anfang an richtig laufen, und die Qualitäts- und Sicherheitsanforderungen in dieser Branche sind hoch. EZ-GO-Checklisten gewährleisten eine einwandfreie Vorbereitung.
TKF stellt Kabel für verschiedene Industrien. In Lochem stellt das Unternehmen dicke Stromkabel her, die auf dem Meeresboden liegen und die dortigen Windkraftanlagen miteinander verbinden. Die Dicke variiert; die Standardlänge solcher Kabel beträgt 8 Kilometer. Ein Kabel besteht aus mehreren Komponenten, die Schicht für Schicht aufgebaut sind. Schließlich werden die verschiedenen Komponenten zu einem Kabel zusammengefügt.
Der Herstellungsprozess sowohl von Bauteilen als auch von Kabeln hat eine wichtige Eigenschaft: Wenn er einmal begonnen hat, kann er nicht mehr gestoppt werden, ohne dass es zu erheblichen Kosten und Problemen kommt. Die 8 Kilometer müssen beim ersten Mal gelingen. Dieser Prozess kann bis zu 16 Stunden pro Bauteil dauern. Deshalb sind die Kontrollen im Vorfeld sehr wichtig. Dazu verwendet das Unternehmen die Checklisten von EZ-GO.
Sjoerd Kleisterlee überwachte als Sicherheits-, Gesundheits- und Umweltbeauftragter (SHE Officer) von TKF die Einführung der EZ-GO-Plattform. Henno Staal ist als externer Berater beteiligt.
“Dank der strukturierten Kontrollen läuft die Produktion ohne Unterbrechung in einem Durchgang”
Sjoerd Kleisterlee: „Neben der Länge gibt es viele strenge Qualitätsanforderungen; es darf absolut nichts daran auszusetzen sein. Liegt ein Kabel erst einmal auf dem Meeresgrund, ist eine Reparatur oder ein Austausch unmöglich oder zumindest sehr kostspielig. Die Qualität dieser Kabel muss jederzeit zu 100 % nachweisbar sein. Auch die Kunden wollen einen Nachweis dafür. EZ-GO erfasst den Nachweis für einen optimal eingestellten Prozess.“
Die EZ-GO-Checklisten werden auch für Sicherheitsüberprüfungen verwendet. Sicheres Arbeiten steht bei TKF an erster Stelle. Man kann sich vorstellen, welche enormen Kräfte beim Aufwickeln und Zusammenlegen dieser kilometerlangen Kabel wirken. Wenn sich während der Produktion etwas löst, ist das lebensgefährlich. Deshalb sind strukturierte Sicherheitskontrollen vor und während des Produktionsprozesses bei TKF von entscheidender Bedeutung.
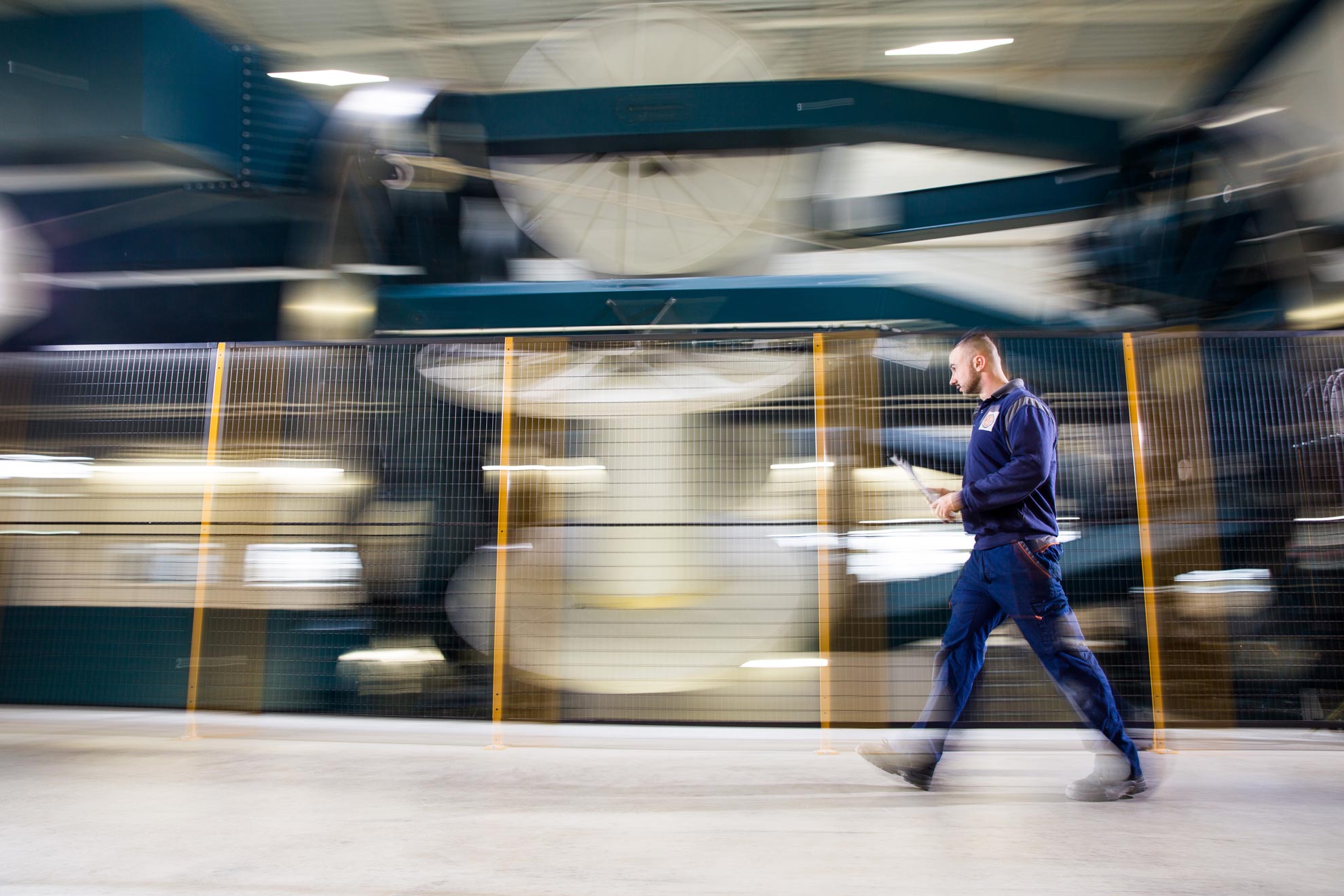
Henno Staal von Produlog begleitet solche Implementierungen häufiger als externer Berater. Er erzählt: „Obwohl TKF mehrere Komponenten der EZ-GO-Plattform einsetzt, wie z. B. Cleaning & Inspection, 5S-Audits und Sicherheitsaudits, liegt der Schwerpunkt auf dem sogenannten 4-Eyes-Check. Das ist die Kontrolle vor dem Start des Produktionsprozesses. Die Person, die die Maschinen einrichtet, führt eine Kontrolle durch, ein Kollege führt dieselbe Kontrolle noch einmal unabhängig durch. Diese gründlichen Kontrollen können bis zu 30-45 Minuten dauern.“
Kleisterlee fügt hinzu: „Zu den Dingen, die dabei abgehandelt werden, gehören die Einstellungen aller Geräte und Maschinen in der Linie, eventuelle Verunreinigungen, die Funktionsweise von Sensoren und verschiedene Sicherheitskontrollen. Die korrekten Einstellungen werden in der App mit Text und Bildern angezeigt, so dass es keinen Zweifel geben kann. Beim Text haben wir sehr auf die Formulierung geachtet. Also nicht: „Temperatur auf 100 Grad einstellen“, sondern „Temperatur auf 100 Grad eingestellt“. Dann kann der Bediener „ja“ angeben und Sie können sicher sein, dass das dann auch so ist.“
Ein wichtiger zusätzlicher Vorteil der EZ-GO-App ist, dass die Checklisten in Echtzeit ausgefüllt und vom Bediener abgezeichnet werden. Kleisterlee: „So kann jeder sicher sein, dass die Kontrollen von zwei Mitarbeitern durchgeführt wurden, bevor der intensive Produktionsprozess beginnt. Wenn jemand eine Anomalie entdeckt, wird sie sofort behoben, aber auch aufgezeichnet. Daraus ergibt sich ein Input für strukturelle Verbesserungen, zum Beispiel wenn eine bestimmte Anomalie häufiger auftritt. Wir halten die einzelnen Kontrollen mit Foto, Datum und Zeitstempel fest. Die Prüfer können diese einsehen. Das gibt auch den Kunden zusätzliche Sicherheit.“