The Lochem-based company TKF manufactures power cables up to 8 km long, which connect offshore wind turbines. There is no room for error in the production process – everything must go right the first time, and quality and safety standards are high in this industry. EZ-GO checklists ensure a flawless preparation.
TKF produces cables for a variety of industries. From their home base in Lochem, the company manufactures thick power cables, which run along the seabed and connect wind turbines. Although the thickness varies, the standard length of such cables is 8 kilometres. The cables consist of several components which are assembled layer by layer. Eventually, the various components are joined together to form the cable.
The manufacturing process of the components and the cable itself share an important characteristic: once started, it cannot be stopped without considerable costs and problems. The entire 8 kilometres must be manufactured perfectly in one go. That process can take up to 16 hours per component. It is therefore very important to carry out checks in advance. For this purpose, the company makes use of EZ-GO’s checklists.
As TKF’s Safety, Health & Environment Officer, Sjoerd Kleisterlee supervised the implementation of the EZ-GO Platform. Henno Staal is involved as an external consultant.
``Thanks to the structured checks, production is not interrupted and perfect the first time around``
Sjoerd Kleisterlee: ‘Aside from the issues involved with the considerable length of the cable, we must also comply with numerous very strict quality standards; absolutely nothing can be wrong with it. Once a cable is installed on the seabed, repairing or replacing it is impossible or at the very least extremely expensive. The quality of these cables must be 100% demonstrable at all times. Understandably, clients want proof of this. EZ-GO records the proof of an optimally configured process.’
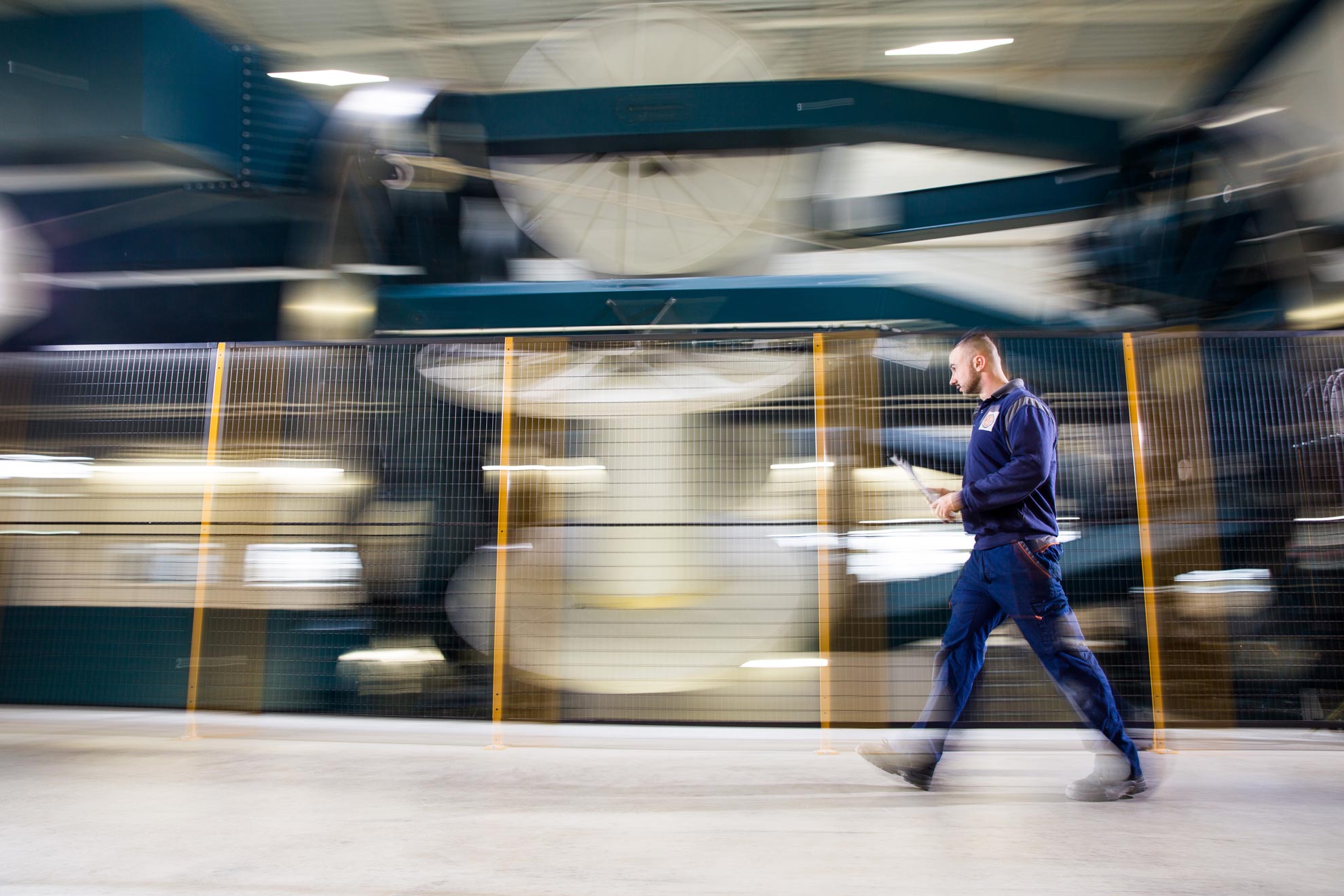
EZ-GO’s checklists are also used for carrying out safety checks. Working safely is paramount at TKF. You can imagine the forces involved in winding and twisting these kilometres-long cables. If something breaks and flies off during production, it could have lethal consequences. This is why structured safety checks before and during the production process are crucial at TKF.
Henno Staal of Produlog is no stranger to supervising such implementations, as an external consultant. He says: ‘Although TKF utilises several components of the EZ-GO platform, such as cleaning & inspection, 5S audits and safety audits, the focus is on the 4-eyes check. This is the inspection before a production process begins. The person configuring the machines does a first check, and then a colleague does the same check again independently. These thorough checks can take up to 30 to 45 minutes.’
Kleisterlee adds: ‘Matters covered include the settings of all devices and machines on the line, possible contaminations, the functioning of sensors and various safety checks. The app points out the correct settings with text and photos, so there can be no doubt about it. As far as the text goes, we took great care with wording. For example, we didn’t write: ‘set temperature to 100 degrees’, but ‘is the temperature set to 100 degrees?’. That way, the operator can say ‘yes’ and you can be sure that that is the case.’
An important additional advantage of the EZ-GO app is that the checklists are completed and signed off by the operator in real time. Kleisterlee: ‘Everyone is therefore sure that the checks have been carried out, by two operators, before the complex production process begins. If someone detects an anomaly, the anomaly is immediately remedied, but also logged. This creates input for structural improvements, for instance if a certain anomaly occurs regularly. We log all individual checks with a photo, a date and a time stamp. They can be consulted by auditors. This way, it also provides clients with extra assurance.’