TKF in Lochem produceert stroomkabels met een lengte tot wel 8 km, die windmolens op zee met elkaar verbinden. Het productieproces moet in een keer goed gaan en de kwaliteits-en veiligheidseisen liggen in deze branche hoog. EZ-GO checklijsten zorgen voor een feilloze voorbereiding.
TKF maakt kabels voor uiteenlopende industrieën. In Lochem maakt het bedrijf dikke stroomkabels die op de zeebodem liggen en daar windmolens met elkaar verbinden. De dikte varieert, de standaardlengte van zulke kabels is 8 kilometer. Een kabel bestaat uit verschillende componenten, die laag voor laag opgebouwd worden. Uiteindelijk worden de verschillende componenten samengevoegd tot een kabel.
Het productieproces van zowel de componenten als de kabel heeft een belangrijk kenmerk: als het is gestart, kun je het niet meer stoppen zonder dat dit aanzienlijke kosten en problemen met zich meebrengt. De 8 kilometer moet in een keer goed. Dat proces kan tot wel 16 uur per onderdeel in beslag nemen. Daarom zijn de checks vooraf van zeer groot belang. Daarvoor gebruikt het bedrijf de checklijsten van EZ-GO.
Sjoerd Kleisterlee begeleidde als Safety, Health & Environment Officer van TKF de implementatie van het EZ-GO Platform. Henno Staal is betrokken als externe consultant.
“Dankzij de gestructureerde checks verloopt de productie ononderbroken in een keer goed”
Sjoerd Kleisterlee: ‘Naast de lengte zijn er ook tal van strenge kwaliteitseisen, er mag absoluut niets mis mee zijn. Als een kabel eenmaal op de zeebodem ligt, is repareren of vervangen onmogelijk of tenminste zeer kostbaar. De kwaliteit van deze kabels moet te allen tijde 100% aantoonbaar zijn. Klanten willen daar ook graag bewijs van. EZ-GO legt het bewijs voor een optimaal ingesteld proces vast.’
De checklijsten van EZ-GO worden ook gebruikt voor veiligheidschecks. Veilig werken gaat bij TKF boven alles. Je kunt je voorstellen dat er bij het wikkelen en samenslaan van deze kilometerslange kabels grote krachten spelen. Schiet er iets los tijdens de productie, dan is dat levensgevaarlijk. Daarom zijn gestructureerde veiligheidschecks vooraf en tijdens het productieproces bij TKF van cruciaal belang.
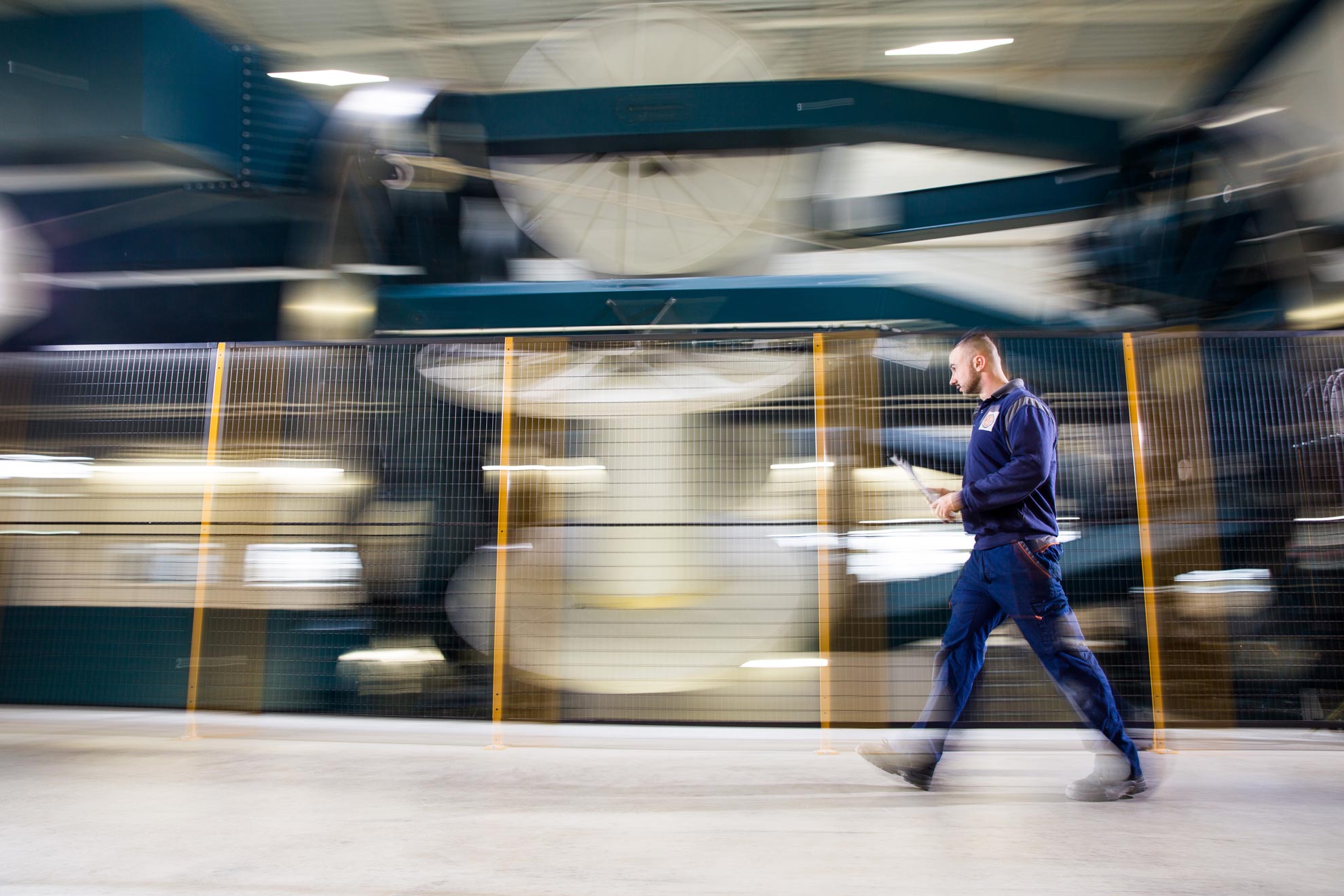
Henno Staal van Produlog begeleidt vaker dergelijke implementaties, als extern consultant. Hij vertelt: ‘Hoewel TKF meerdere onderdelen van het EZ-GO platform gebruikt, zoals cleaning & inspection, 5S-audits en veiligheidsaudits, ligt de nadruk op de 4-eyes check. Dat is de controle voordat een productieproces gestart wordt. Degene die de machines instelt, doet een check, een collega loopt dezelfde controle nog een keer onafhankelijk na. Deze grondige checks kunnen wel 30-45 minuten duren.’
Kleisterlee vult aan: ‘Zaken die daarbij aan de orde komen zijn onder andere de instellingen van alle apparaten en machines op de lijn, eventuele vervuiling, de werking van sensoren en verschillende veiligheidschecks. De juiste instellingen zijn in de app aangegeven met tekst en foto’s, zodat er geen enkele twijfel kan zijn. Bij de tekst hebben we veel aandacht besteed aan de formulering. Dus niet: ‘temperatuur instellen op 100 graden’, maar ‘temperatuur ingesteld op 100 graden’. Dan kan de operator zeggen ‘ja’ en weet je zeker dat het zo is.’
Een belangrijk extra voordeel van de EZ-GO app is dat de checklijsten real time worden ingevuld en afgetekend door de operator. Kleisterlee: ‘Iedereen weet dus zeker dat de checks zijn gedaan, door twee operators, vóórdat het intensieve productieproces start. Als iemand een afwijking constateert, wordt die direct verholpen, maar ook vastgelegd. Zo ontstaat er input voor structurele verbeteringen, bijvoorbeeld als een bepaalde afwijking vaker voorkomt. De individuele checks leggen we allemaal vast met een foto, een datum en time stamp. Auditors kunnen die raadplegen. Zo geeft het ook aan klanten extra zekerheid.’