Intelligent factories are the future. Thanks to new technologies such as artificial intelligence (AI), Internet of Things (IoT), virtual reality, cloud technology, robots and advanced analytics, we can automate ever more parts of the production process. But where does one start?
Even though no-one says this out loud, most companies are a far cry from reaching Industry 4.0 and can’t really be called smart factories yet. Human input is a major part of most production processes and machines cannot be replaced just like that: production tools require substantial investments that are made for the long term.
It all sounds very appealing: a factory without people, in which all the machines work silently, managed by artificial intelligence which knows exactly what needs to be produced and how, and which digitally controls the machines to do so. There is an expressive term for this: lights out.
The importance of Industry 4.0
Working towards Industry 4.0 is an urgent matter. Good production staff is hard to come by at the moment and it doesn’t look like this will get better any time soon. On top of that, the pandemic has left many companies reluctant to have large concentrations of people on the work floor. Using cheap labour in faraway countries is also becoming less attractive; right now, because of increased transport costs, but in the long term also because of considerations of social responsibility and sustainability. Reshoring is the trend, but how do you ensure reliable production in a region where labour is expensive, if you can even find people at all? The obvious thing to do then, is to invest in smart production facilities.
Smart manufacturing
Smart manufacturing, however, is not something that happens with a Big Bang. It’s something you do step by step. Therein lies the challenge and the success of a transition to smart factories. The main thing is to connect the digital and physical worlds. For example, by allowing order pickers to use advanced scanning techniques, RFID and voice control. Or, by using AI to improve demand forecasting and planning. By considering the possibilities of connectivity when purchasing new production resources, you will increase the smartness of your factory while guaranteeing its continuity.
Start with the basics: facilitate the operator
One of the most underestimated tools for facilitating Industry 4.0 is operator software. At present, even the most advanced factories still employ a high number of operators. After all, machines need to be operated, calibrated, cleaned, inspected and so on. In factories where machines are more intelligent, the demands on operators are even greater, as they have to perform more advanced tasks and deal with smart software. It is expected that operators will continue to play an important role in the production process for a long time to come.
EZ-GO is a platform that has been fully developed to support operators. In many factories, work instructions and checklists are still printed out in binders. That is inefficient (‘Now where did those instructions go?’), unsafe (‘I don’t feel like getting the binder, I’m pretty sure I know what to do’), time-consuming (retyping checklists) and imprecise (‘That is such a long story, I’m not sure what the point is?’). The quick win for smart manufacturing lies in good operator software that facilitates all this.
Digital, visual, on-site
The heart of EZ-GO is an app which runs on tablets, which are always available at the production site. The app shows exactly what needs to be done for each shift and the digital work instructions make use of photos and videos. If operators observe any abnormalities, they can report them immediately using the app, thereby preventing potential problems.
Checklists, audits and other documents are digital as well. A major advantage of that is that the results immediately get recorded in the main EZ-GO platform and can easily be analysed to facilitate continuous improvement.
Immediate results
Industry 4.0 starts with the basics: facilitating processes with digital tools that immediately improve production processes, as well as familiarise operators with digital tools and show them how technology makes their work more fun, easier and more interesting. It gives more autonomy to the operator, who can therefore work more effectively. This has an immediate positive impact on the safety, quality and efficiency of the entire production process. Ultimately, this is the aim of any intervention in production facilities, whether you call it smart manufacturing, Industry 4.0 or simply automation.
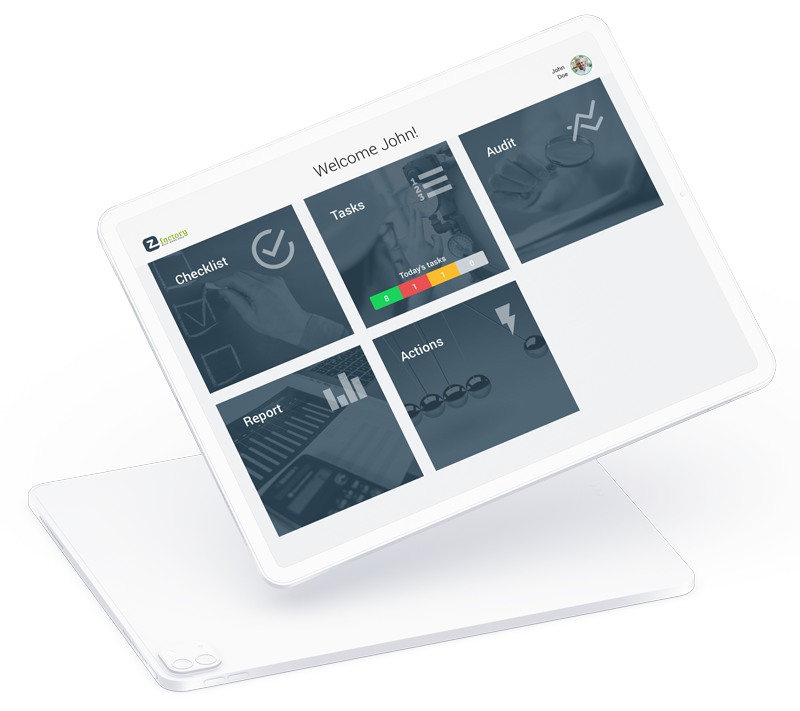
About EZ Factory
EZ Factory develops innovative and user-friendly apps to support and optimise operational processes in industry. These ‘bottom-up’ tools allow operators, team leaders and mechanics to work more efficiently and to continuously improve processes. Checklists, work instructions, autonomous maintenance tasks, training courses and audits become simpler and are better visualised. Results are immediately available in a dashboard. The EZ-GO app is already being used by renowned companies such as Heineken, FrieslandCampina, BMW and Jacobs Douwe Egberts. EZ-GO simplifies the work of frontline workers and enhances the safety, quality and productivity of production. EZ Factory believes in the strength of the people making the products and always develops apps from their perspective. That is why the motto is: Power to the operator!