The Hoogvliet bakery supplies its stores multiple times a day with a wide and fresh assortment of bread. The working methods on the various production lines were mainly in the minds of experienced employees. With EZ-GO, Hoogvliet has now documented the best practices. The enthusiasm of operator Agnieszka, who led the implementation, was a key success factor.
Bakery manager Gerald Willemsen, production team leader Tom van Dijk, and packaging operator Agnieszka Wojcik explain how they collaborated to implement EZ-GO.
Hoogvliet holds a unique position as the only Dutch supermarket with its own bakeries linked to distribution centers. This allows Hoogvliet to deliver fresh bread to its branches multiple times a day. The experienced operators are the bakery’s most important asset. However, Gerald Willemsen was uncomfortable with the fact that their knowledge of production settings, conversions, and working methods was scarcely documented.
Willemsen: ‘We didn’t even have our basic settings on paper. All that information was in the heads of the employees. This makes you vulnerable. Moreover, everyone had slightly different views, which sometimes led to discussions. We always want to work in the best possible way. I wanted to document that best practice. We chose EZ-GO because their system is designed from the operator’s perspective. Operators can create tasks, work instructions, and checklists themselves, which is the great strength of this platform. This also ensures buy-in.’
``All operators are happy with it``
Operator Agnieszka Wojcik was immediately enthusiastic about the platform and was tasked with leading the implementation. ‘For my own packaging department, I could fill in almost everything myself, as I had that knowledge,’ she says. ‘For what happens in other departments, such as production, I spoke with the operators and team leaders there.’ Team leader Tom van Dijk: ‘I explained how a certain process works in the factory, and Agnieszka documented it in the app.’
Agnieszka: ‘It was a lot of work to create the accompanying photos and videos, but it was worth it because it clearly shows what needs to be done at a glance. Additionally, the texts are written in two languages: Dutch and English.’
Willemsen: ‘We started a pilot in November 2023 on one of our three production lines for eight weeks. After that, we conducted a survey among the operators, which showed a lot of enthusiasm. It was really the right way to work. We then decided to expand; since April 2024, we have been working with tasks, work instructions and checklists on all lines. We plan to set up audits next. I also want to work on the digital skills matrix. Soon, we will start a technical training for autonomous maintenance, and I would like to document such matters better.’
You don’t determine a best practice alone. Agnieszka therefore always asked different operators how they work before documenting it in the app. This sometimes led to discussions, says Willemsen: ‘Agnieszka doesn’t have a managerial position and can’t make that decision alone. When different people had different ideas about the best way to work, we decided together. There is ultimately only one best way of working. It is now accessible to everyone. If there is ever a discussion about it, you can simply refer to the work instruction. This is also very useful for training new people.’
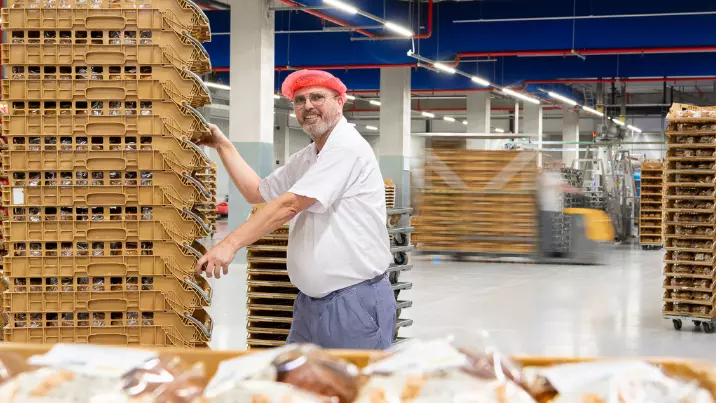
Recurring tasks are now documented, as are checklists and work instructions. Additionally, operators use the option to create actions if they encounter something unusual. Van Dijk: ‘The enthusiasm for this was so great that we had to filter it a bit at first. Not every point is an action. It’s running smoothly now.’ Willemsen believes that more should be done with this information in the company. ‘These actions are relevant and meant to be resolved. So, you have to resolve them. The team leaders haven’t fully grasped this yet. We now address this by reviewing the list of actions during work meetings and deciding together what needs to be done for each action. Then it’s quickly resolved.’
It was a bit of a search at first: what exactly is a task, when do you use a checklist, and what are work instructions for. Willemsen: ‘We hadn’t fully understood all the possibilities of the app. After the pilot, we asked for additional support from EZ Factory, which now allows us to make optimal use of all the platform’s functionalities. They also helped us look beyond just the app itself. For example, how to use the app in communication between team leaders and operators, or what you can do with the reports.’
‘We’re not there yet,’ says Van Dijk. ‘When you use such a platform, you must realize that it doesn’t run itself. You have to fill and maintain the system properly. You have a certain goal with it, and it’s important to keep that in mind. We mainly wanted to document and make the knowledge of our operators accessible in a user-friendly way. We succeeded.’ Willemsen concludes: ‘We also find it very important that the system contributes to job satisfaction. It ensures that everyone knows what is expected of them, and there is less discussion. EZ Factory says “Power to the Operator”, and that’s exactly what we achieved. That’s the main advantage of this platform for me.’