VISTA college in Limburg (NL) trains young people to become operators in the industry. Since September 2024, the school has been using EZ-GO in its practical lessons. Training manager Marc Konings says: ‘Industry is becoming more digital, and students need to be prepared for that. With EZ-GO, they can familiarize themselves with a factory, perform inspections, and improve processes. It also aligns perfectly with this generation.’
VISTA college offers a wide range of vocational (MBO) programs, including training for the next generation of process operators, both for the process and food industries. Smart Maintenance is also a key component of this program.
Training Manager Marc Konings and volunteer Ton Kitzen share how the EZ-GO platform adds value to the process operator training program.
Marc: ‘We’re seeing industrial environments becoming increasingly digital. That’s the future. It’s important to us that students learn based on tomorrow’s industry, not yesterday’s. That’s why we use QR codes, websites, 3D technology, and now also EZ-GO.’ Ton adds: ‘The average student is 16 years old, they’re digital natives and very comfortable using tablets. Reading and writing things down isn’t very popular with this generation. That’s why EZ-GO is such a great fit. They check, click, and they’re done. Work instructions are easy to follow with photos and videos. And everything a student does in EZ-GO is digitally recorded. It’s a huge step up from walking around with paper checklists that often never get digitized.’
``Our students are the early adopters of EZ-GO, making them especially valuable to the food and process industries.``
The training setup at the college simulates a realistic factory environment. Since September 2024, students have been using EZ-GO on-site. Ton: ‘We use it in several ways. First, it helps new students get to know the factory, just like in a real company. You could say: here’s a tablet and a cap, and you’re good to go.’ Marc adds: ‘We also use it for work instructions, inspection rounds, 5S audits, routine audits, and maintenance. We keep expanding its functionalities, EZ-GO offers everything you might need.’
The maintenance feature serves two purposes. On one hand, students can identify issues during inspections, resolve them, and record everything in the platform. If another team member needs to take action, they can create a report in EZ-GO with a photo and a brief explanation. Maintenance students can then follow up on these issues. Ton: ‘Anything a student hears, smells, or sees that’s unusual can be easily reported. That helps prevent problems. If someone notices a pump vibrating more than usual, a technician can step in before it breaks down, avoiding costly damage and downtime. That’s exactly what our students are learning.’
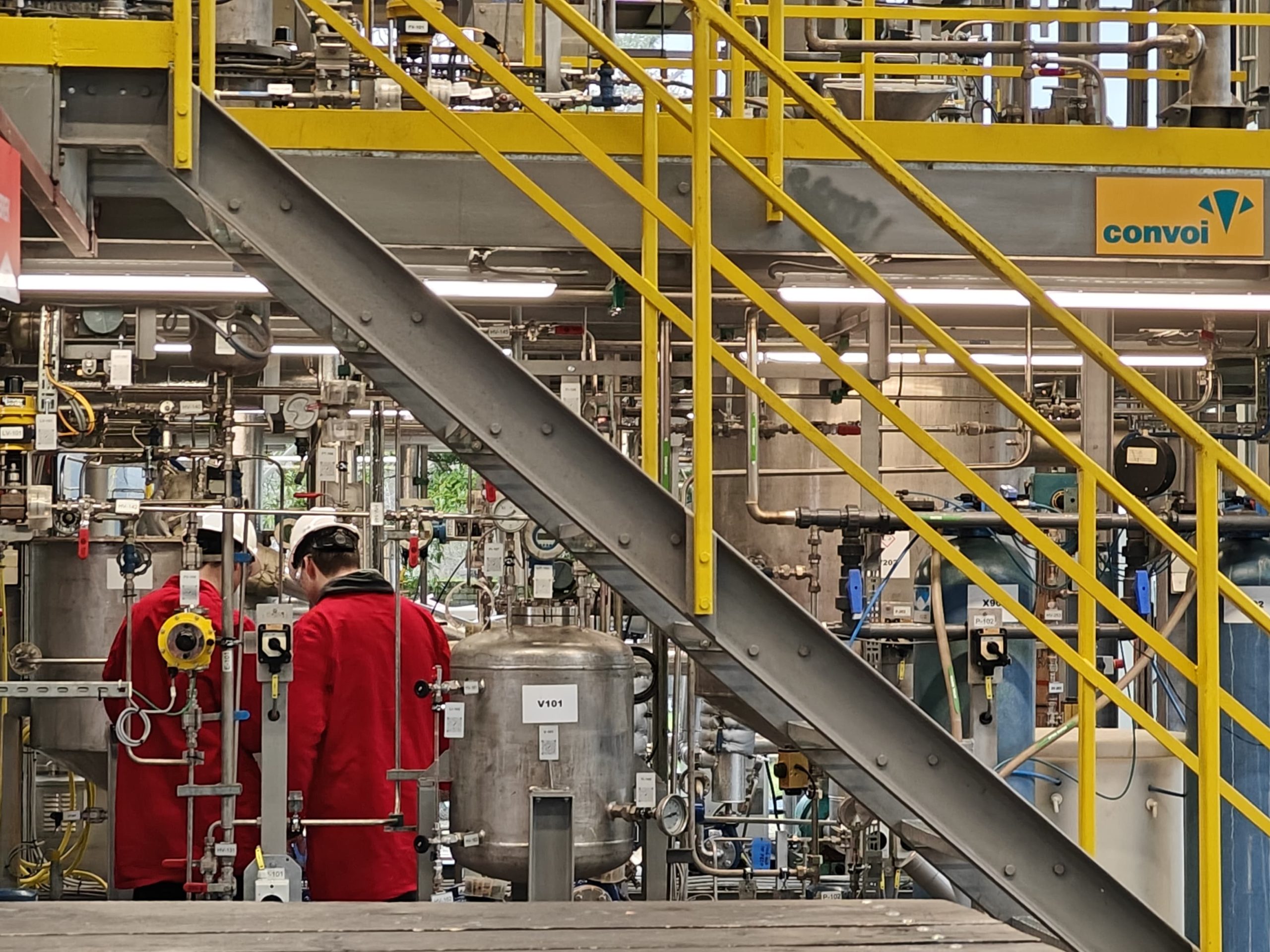
As the industry evolves, data is becoming increasingly important and must be properly recorded. Marc: ‘The data an operator logs may well be the most valuable part of their job. AI can use that inspection data to predict when maintenance is needed or detect patterns to optimize processes. Companies care about this because they must operate more efficiently. At VISTA, students learn how to record data in EZ-GO in a structured way and why it matters. They understand how that data is used and how it helps improve operations.’
Some companies still rely on paper checklists. Marc: ‘There’s nothing inherently wrong with that, but using a digital platform like EZ-GO is more efficient. It also helps preserve operational knowledge, especially through work instructions. That knowledge becomes accessible to everyone in the organization. Our students are early adopters of these new technologies, making them even more valuable to the food and process industries.’
Ton offers one final note: ‘Human behavior is still the most important factor. A platform like EZ-GO only works if people use it. Fortunately, EZ-GO is very user-friendly. It’s so intuitively structured that it’s almost impossible to get it wrong. Once it’s set up, it works for everyone, even those with limited reading skills, dyslexia, or social anxiety. Students tell me they really enjoy working with it, and we see their motivation and self-confidence grow.’
EZ-GO at VISTA college was implemented with input from the students, making them the first users. Ton: ‘This means they also think about how processes work and why, what checks are needed, and what happens with the data. They apply this both in the food and process industries, which each have their own priorities. That kind of insight is incredibly valuable.’ Marc concludes: ‘Working with EZ-GO already benefits our students, they learn a lot and enjoy using it. Soon, they’ll bring these advantages with them into the professional world. And that benefits everyone.’