Optimisation and continuous improvement. Two expressions that are important to both organisations. But they have a different meaning for both organisations. EZ Factory specialises in developing a technical solution to make the work of operators in a factory easier. Perfact specialises in analysing processes and optimising them. We do this mostly through the globally proven Lean Six Sigma methodology. Together, EZ Factory and Perfact join forces to be able to do even more for a client.
Continuous improvement
“Lean Six Sigma is an approach that we apply to organisations in order for them to achieve concrete results in the area of process improvement in a structured manner. We do this through the DMAIC principle (Define, Measure, Analyse, Improve, Control)”, indicates Bas Mooij, Lean Six Sigma Master Black Belt at Perfact.
In the first phase, the problem definition and critical success factors are defined. “These are measurable characteristics that provide insight into the process performance. Then, based on the measurements, we analyse further for possible reasons that influence the critical success factors. When we have identified these reasons and their effects, we use them to identify the cause of process problems and then take improvement actions,” continues Bas.
In the final phase, the process control system is adjusted so that the process continues to perform at the improved level and can be secured for the future. The collection of data from the production process as well as the correct and long-term securing of the improvement proposals made is a labour-intensive job. “Think of the operational tasks that come with paper checklists, the data that is located in numerous places and interrupting the work for interviews. This cannot really be called efficient. This can be improved and the technical solution developed by EZ Factory can help,” says Coppe Sturmans, Director Perfact.
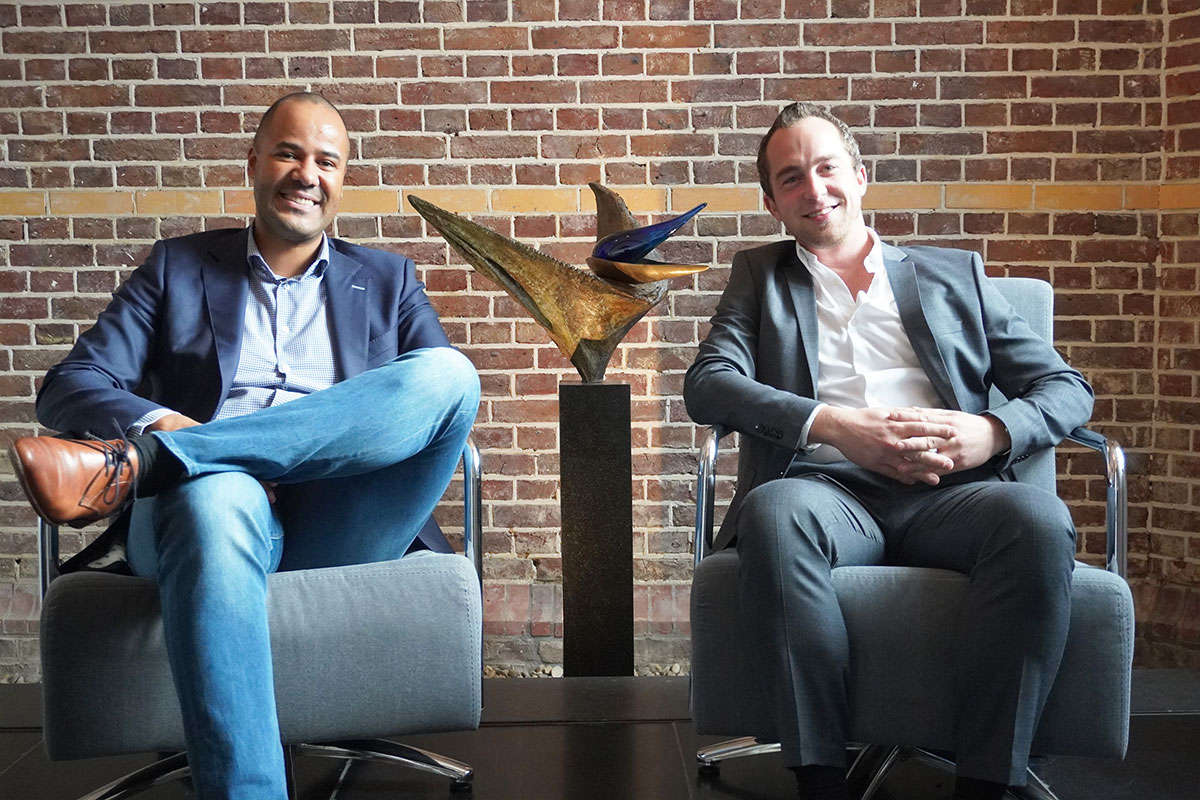
Operators to the power
EZ Factory developed a technical solution in the form of a single integrated platform (EZ-GO) to digitise operations and empower operators. “This empowers them to take the lead in continuously improving their own processes, or so to say continuous improvement,” indicates Randy Appiah, Founder of EZ Factory.
The simple and visual app is a mobile solution and is used in production environments to digitise checklists, work instructions, first-line maintenance tasks and audits. “This makes the EZ-GO platform a nice mobile solution that offers the possibility of very targeted continuous improvement in production environments. In addition, the application offers the possibility of setting up work instructions and proposing improvements to the standard by means of an action and chat module,” Randy continues.
“We will use the tool initially as a pilot to collect data prior to an optimisation process and after completion of a Lean Six Sigma analysis to secure the defined improvements. In this way a continuous improvement loop is created and together we make the difference for our customer”, Coppe concludes.