As a producer of infant and elderly nutrition, Dutch Nutrition/FrieslandCampina must comply with strict legal food safety requirements. It is vital that every process is carried out carefully and consistently, something that’s guaranteed with the EZ-GO platform. The platform also communicates seamlessly with the company’s other quality and maintenance systems.
Dutch Nutrition is a young company started in 2018 that produces powdered food for infants and the elderly. Their product serves the most vulnerable in our society, so food safety requirements are strict, and rightly so. It is important to secure processes and demonstrate that security within frameworks like HACCP requirements.
“We always want operators to carry out tasks in the same way, at the right time,” says quality manager Dick de Vries. “Skipping a task or doing it slightly differently can have major consequences. We’ve included all of our tasks in the EZ-GO platform, including inspections and calibrations that may only need to be done once a year. It’s those kinds of processes that could otherwise be easily forgotten. The instructions are recorded as short videos or one-point lessons, and step-by-step photos explain how the operator should perform a certain action.”
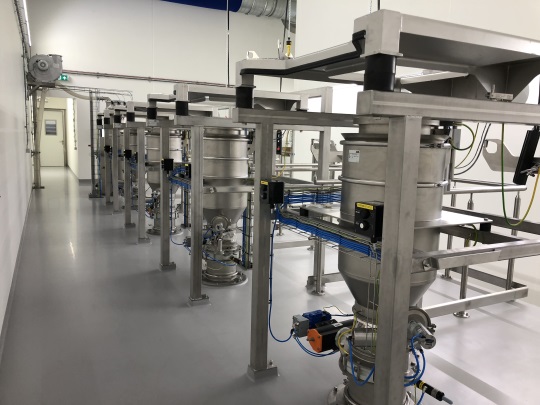
Of course, the company already uses multiple different systems. The HACCP requirements are largely incorporated into the system that controls production processes, DPS. EZ-GO is a digital tool that Dutch Nutrition uses to keep the machinery in optimal condition and prevent errors and downtime as much as possible. “The EZ-GO platform is like a shell around DPS and supports the operators in the various steps,” explains De Vries. “The systems really complement each other – the underlying data from both systems provides a solid foundation for continuous improvement. For instance, if DPS registers a standstill, you can link it to the checks in the EZ-GO data. When were the checks carried out, with what frequency, and could there be a reason to adjust it? It allows you to continuously improve the processes.”
“EZ-GO is a digital tool that Dutch Nutrition uses to keep the machinery in optimal condition and prevent errors and downtime as much as possible.”
Dutch Nutrition brought in an external consultant to help with implementation: food technology and process engineering specialist Ellen Grashof. “In the beginning, we had more people involved, but it turned out to be more effective for us if one person was focused completely on filling the system, while simultaneously checking to see if our methods were the best they could be,” says De Vries. EZ Factory and implementation partner Pontifexx provide technical and procedural support. “It’s important to have a clear structure from the outset,” Grashof explains. “What is a checklist, what is a task, what do you record. Pontifexx helped us to keep those things in focus.”
Grashof explains that she works closely with the operators and team leaders. “I go out onto the floor and literally stand next to the operator and ask them: show me how you dismantle the filling head or how you replace a gasket. I record every action. I take photos of each step and ask them what could go wrong, what we should pay attention to, and if we could do it better. It’s important for me to take a critical look at the way the work is done with the people who do it, so I can adjust it and the correct procedure can be entered into the EZ-GO platform. Of course, I also coordinate with the team leaders and QA. The next step is making the system better and better by using the improvement circle, because good can always be better. The operators actively use the content in the EZ-GO app and can use the app on the iPad to let us know if a method or photo needs to be adjusted. It helps us work smarter. Every tasks from every department is now available on the EZ-GO platform.”
But that doesn’t mean that Dutch Nutrition is resting on its laurels. “Firstly, we are continuing to improve processes,” says Grashof. “If an operator encounters an error, they can report the solution in EZ-GO as a task. Let’s say a clogged filter keeps causing errors, then the operator can indicate that the filter needs to be cleaned or replaced more often. That keeps the problem from recurring. Secondly, we’ll be using the audit function to test employees’ knowledge, so we can ensure that they always have adequate control of their machines. We then have that information to show external auditors, as well. We will also continue with tasks from the Technical Department. That certainly isn’t the finish line, we are constantly discovering new opportunities.”
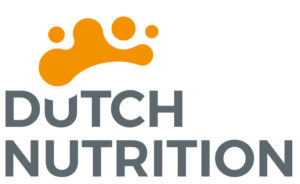
When we spoke to Dutch Nutrition, the app had only been operational for a month, but the initial results were already visible, according to Dick de Vries. “It’s easy for the operators to use the iPad, and they’ve also started to recognise the added value, even though it took them a while to see it. Up to this point, they had always done things by memory. Now the operators are starting to appreciate the reminders, and noticing the practical impact: for instance, they’re no longer missing tools, because they are always in the same place. It also helps that they can make suggestions for improvements themselves – the platform invites interaction. And it takes work off the team leader’s plate – he now has a clear overview of the tasks and checks that have been carried out and can provide more targeted direction for the team. But perhaps the most important thing is that we now have a tool that allows us to guarantee that all the process steps are always done in the same way, at the right time.”