On a beautiful November day in 2016, we stood outside Grand Café Oosterbeek after a spectacular lunch, high-fived, and promised that we’d each put some money in the pot and go for it.
Five years and several investments later we have many satisfied clients, and we’re determined to make EZ-GO the number one software platform for people in factories. We’ve stayed true to our motto, Power to the Operator, and created software that gives them this power and makes their whole business better while remaining as simple as possible. Johann Cruijff said playing football is simple, but playing simple football is the hardest thing there is. The same is true when it comes to making software.
When we met, Robert as a consultant and Randy as an autonomous maintenance specialist with a dairy company, we immediately clicked. Randy was looking for a way to simplify autonomous maintenance, but it wasn’t easy. Operators were doing their level best, but their lists and instructions were scattered all over the place: on paper, in binders, in Excel.
The operators used checklists to an extent, but the information wasn’t stored anywhere. We dreamed of a central database where all the standard daily tasks would be kept, including autonomous maintenance and 5S. All the relevant information would be in one place. Robert was the first to understand what Randy meant, and be able to build it.
But it still wasn’t a done deal. In the first instance, Randy couldn’t get Robert’s quote signed off by the company, and people told him they’d always done it on paper before, and it worked fine. Then the CEO told Randy at an employee breakfast: “If you believe in it, just go ahead and do it. The worst that can happen is you get your knuckles rapped.” That afternoon, he signed the quote himself.
Alpha version
Robert was delighted to find someone on the same wavelength as him. There weren’t many people who shared his vision and understood the need for this product. We’d both spent many years walking around on the shop floor, and knew exactly how important operators and team leaders are, and the kind of issues they face each day.
We also know that it doesn’t work to try and improve their efficiency on a top-down basis. They can do it much better themselves, bottom up. The system we built for that dairy company was basically the alpha version of EZ-GO. We were still using Excel for it, but at least it was standardised and centralised.
Entrepreneurship
We didn’t want to stop there. We saw we had something unique in the making, and we wanted to help more people, because we know how hard being an operator can be. We had the answer, and we were sure there was a lot more we could do with it. Not by making it bigger or more complex, by but by simplifying.
We began developing what is now the EZ-GO platform in 2016, alongside our normal jobs. We officially set up our business in July 2017, and by January 2019 we’d made enough progress to stop doing other work. Overnight, we went from a really good salary to nothing. We didn’t earn a penny for a long time, and the money we did have was put into developing EZ-GO.
As entrepreneurs, we believed in the four Ds: dream, decide, do, and don’t give up. Most importantly, don’t spend too long thinking: if you know you need to put something together, go for it. And don’t give up, because there will always be setbacks. If it was easy, someone would probably have done it already.
Believers
We’re very grateful for our first and second clients: they were important turning points for us. The first was Co Bakker, of the overhead door manufacturer Flexiforce. In April 2017, based solely on the prototype, he said: “We want that. Just build it, and I’ll help you test and debug it.” Shortly afterwards, it was up and running.
When we got our second client, we knew there was no going back. It was Phillip Morris. Their operators would be using our app 24/7, and they have good legal people who drew up a watertight contract, so we really had to have all our ducks in a row. We walked out of the door, looked at each other and laughed out loud. Because now things really had taken off.
Development
Like all startups, we’ve had our setbacks, but we don’t dwell on them too much. Basically, this system has been built three times by different parties. Not until our own team Flex force built it the third time did we have a really stable version that we could confidently build on.
We now have a chief technology officer, and an internal design team that builds all the crucial components. We outsource some of the programming, but we keep a close eye on it. Stability is one of the most important characteristics our system must offer, and it does. If a company’s operators work 24/7, our software must too.
Pedestal
Power To The Operator is not just a slogan: we really do put them on a pedestal, and we think that’s logical. Operators are the men and women who ensure that high-quality products get made every day, food is safe, and batches of products we use on a daily basis keep rolling off the production line. Some people say robots are taking over. Of course, there are a number of processes that are best automated: packing boxes is increasingly done by machine.
But robots have to be controlled. And they don’t clean, maintain, calibrate or repair themselves. People will always be a crucial part of the production process, and you need to make their jobs as easy, pleasant, and effective as possible. You have to do your best for them, and look after them.
Simple and focused
When we developed EZ-GO, we went into the factory with an A5 notepad, the same size as a tablet, with a tablet actually drawn on it. Then we asked operators what do you need, what should it look like. They have the knowledge, and you should leave it to them. A lot of what you now see in EZ-GO is the result of these sessions.
There were three important things we heard again and again:
“I don’t want to see everything, just what’s relevant to me at that moment.”
“Could you make it more visual? It’s a real slog wading through all those written instructions, particularly for my Hungarian/Polish/Eritrean/Spanish colleagues.”
“The simpler the better: If I need a manual just to understand the system, it’s not serving its purpose. It must be immediately clear what I have to do.”
These three principles are still at the heart of EZ-GO: everyone gets the information he or she needs, when they need it, and visually where possible. The app must be intuitive, even for an operator on their first day.
We’re still trying to achieve that on a daily basis.
Only manufacturers
A lot of people have tried to sidetrack us – they say wouldn’t this technology be perfect for healthcare, construction, catering, hospitality – and of course that would be fantastic. But we’re specialists in manufacturing, we know all about production processes, and that’s what we concentrate on. We’ve found the biggest challenge as entrepreneurs is focus, so we stick to our what we’re good at.
As part of this, we support the whole process of operational excellence: carrying out work and maintenance tasks, but also tracking, reporting and solving problems, monitoring standards, training people, and improving processes.
Looking ahead
Within this domain, we’re continuing to develop the EZ-GO platform based on where our clients are going. We don’t make everything they want, because nobody wants a system with a hundred add-ons. Fortunately, they can configure the platform themselves and add working instructions for autonomous maintenance or other tasks such as startups, retooling, and transfers. They can set up their own checklists and audits within the system.
We don’t facilitate things where there are already perfectly good systems, but we are working on interfaces with those systems, such as maintenance, ERP, and quality software. We’re making it easier to analyse the data on the platform and link it to other databases.
One relatively new feature there’s been a lot of demand for is a skills matrix that shows at a glance who can do what: this is particularly useful for scheduling and training plans. Everything we add is built on the same sound basis and the same principles: it’s simple, visual, and aimed at the heroes who work in factories.
Connected worker software
In five years, we want to be in the European top three and the global top ten for connected worker platforms, which is what they’re called now.
Basically, in five years, we want to make the jobs of factory operators, team leaders and managers worldwide safer, easier, more efficient, and more enjoyable. We want to give them more easiness. Yes, that’s another term, but it’s our term. It means the EZ-GO platform is based on a smart and complex system, but on the surface it’s simple. It’s very easy for a factory to implement and roll it out to other factories. And it’s easy for people to use, because that’s what it was developed for: power to the operator.
Robert Bouwman
Randy Appiah
Founders, EZ Factory
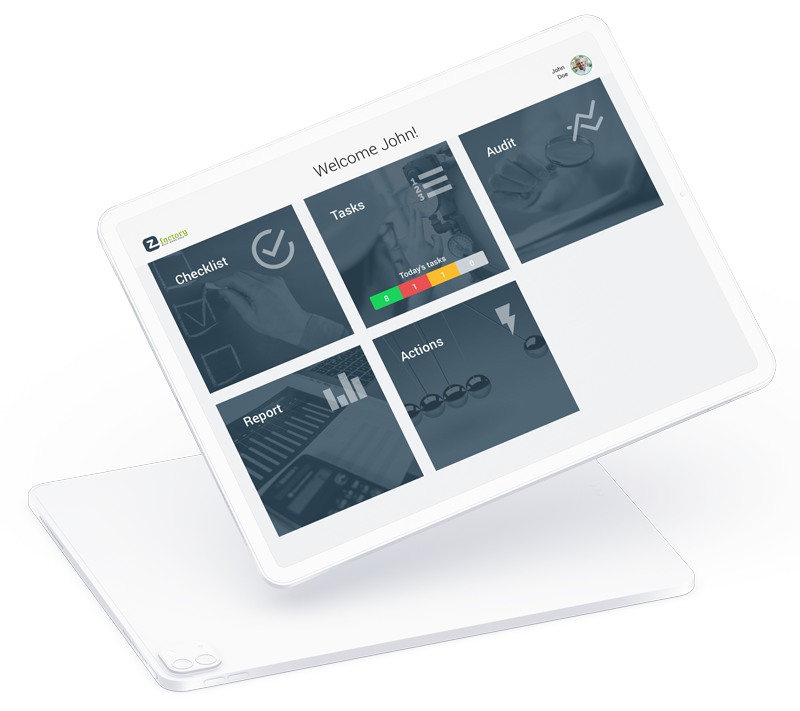
About EZ Factory
EZ Factory develops innovative and user-friendly apps to support and optimise operational processes in industry. These ‘bottom-up’ tools allow operators, team leaders and mechanics to work more efficiently and to continuously improve processes. Checklists, work instructions, autonomous maintenance tasks, training courses and audits become simpler and are better visualised. Results are immediately available in a dashboard. The EZ-GO app is already being used by renowned companies such as Heineken, FrieslandCampina, BMW and Jacobs Douwe Egberts. EZ-GO simplifies the work of frontline workers and enhances the safety, quality and productivity of production. EZ Factory believes in the strength of the people making the products and always develops apps from their perspective. That is why the motto is: Power to the operator!