Solar shading manufacturer Kvadrat Eibergen is experiencing rapid growth, and currently training a new generation of operators with EZ-GO. In addition, the company is facilitating autonomous maintenance and continuously improving production processes.
‘When I ask my children how to do something, they refer me to YouTube’ says Detmar Roessink, Managing Director Shade at Kvadrat. ”The paper world is not the way of the future. You can never explain something as clearly on paper as you can with videos and photos. Which is why, when we were looking for a solution to schedule autonomous maintenance and transfer know-how, we knew it had to be in digital and visual form.’
Kvadrat Eibergen manufactures solar shading products. The weaving of the cloth, metallisation of the fabric and assembly into complete solar shading products all take place at our own locations. ‘We are a genuine craft firm,’ continues Detmar. ‘Our experienced employees have a lot of know-how, and their average age is high. Right now, we’re experiencing rapid growth, so lots of new, young people are joining us. However, we didn’t really have any proper training material to deal with this influx. With EZ-GO, we have found an excellent solution.’
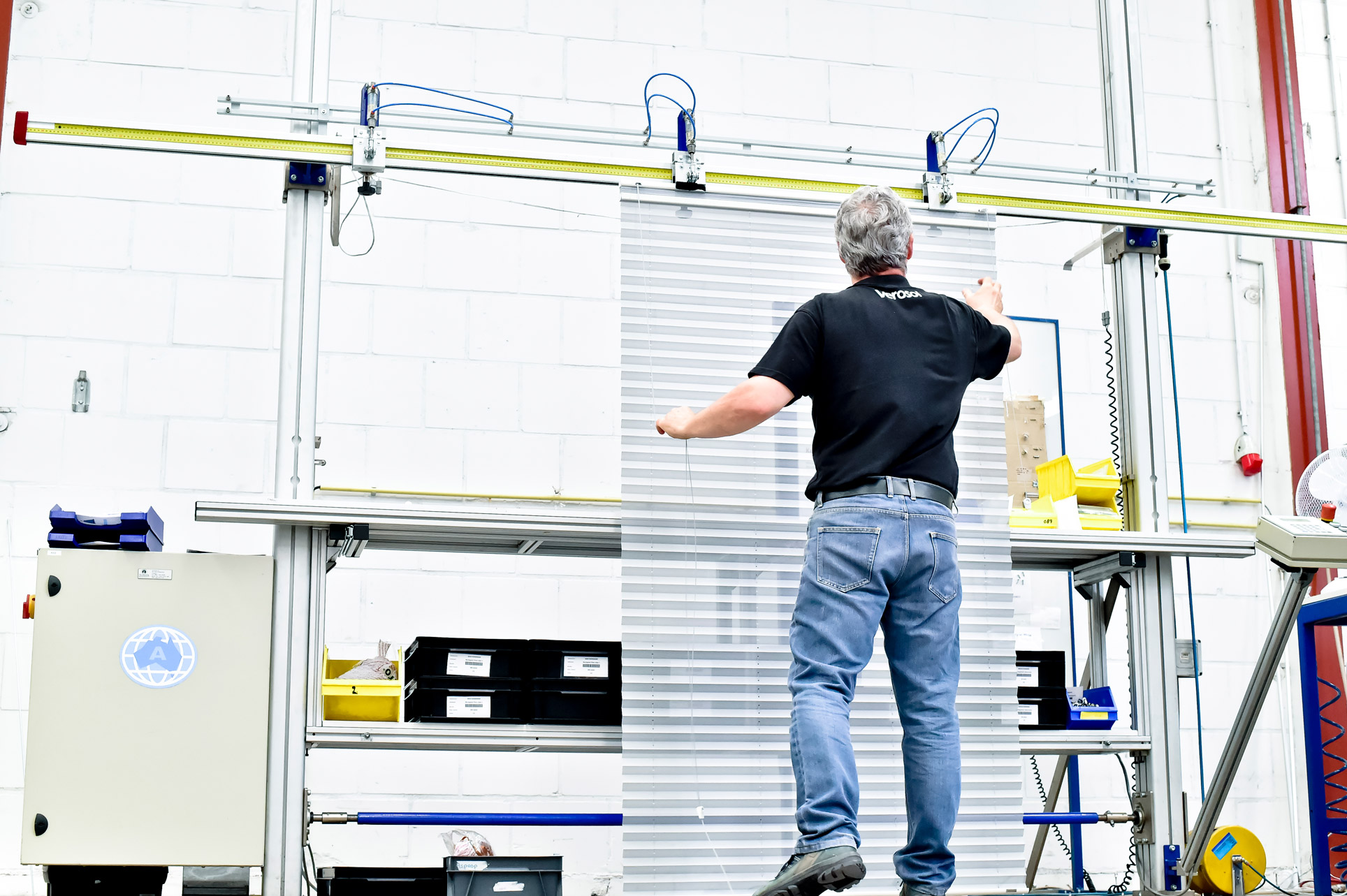
Another important reason to start working with the platform is that there was little structure to scheduled activities such as cleaning, inspection and maintenance. Detmar: ‘I am really someone of the TPM school (Total Productive Maintenance), and believe in autonomous maintenance by the operator. But this is something you have to facilitate. This platform also provides the opportunities for it.’
“I am really someone of the TPM school (Total Productive Maintenance), and believe in autonomous maintenance by the operator. But this is something you have to facilitate. This platform also provides the opportunities for it.”
In the Netherlands, Kvadrat has three production sites: for weaving, metallising and assembly respectively. The implementation of EZ-GO at these locations is led by Kilian Bennink, as part of his role as Supply Chain Manager. ‘In March 2021, we commenced operations at the plant where we metallise fabrics. These are batch processes with rolls of fabric of up to 4,000 metres. The existing work instructions hadn’t been revised for a long time – with many not recorded at all -, so we started with these. We began by looking at the two most complex machines. After revising the work instructions, the actual filling of the app with text and images required very little subsequent work. For these machines, everything took two days. This was followed by the roll-out to the other machines and the use of more functionalities from EZ-GO. We also include 5S audits in the app, for example.’
The other locations followed. At each location, the project leader initially gives a presentation to show what the EZ-GO platform entails, and how it can be of use to the operators. The project team organising the implementation always includes a team leader and some operators. After all, they know the processes and, most importantly, exceptions. Kilian’s role is diminishing with each location, he says: ‘I am currently training someone to manage the project at the weaving mill.’ Implementation will start there in December 2021.
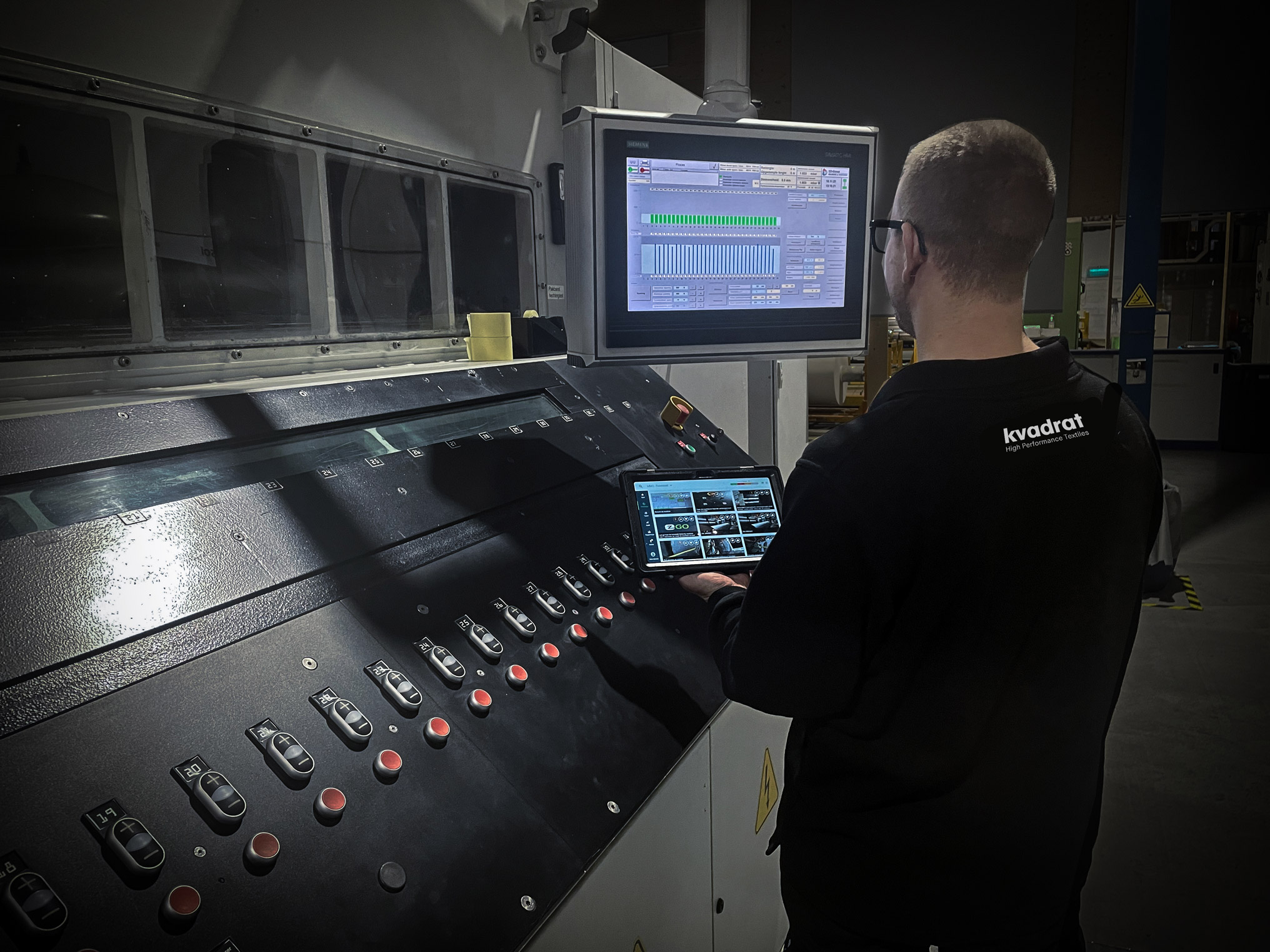
There are two sides to training employees with EZ-GO. Firstly, the checklists and work instructions are used on site when training new employees. Secondly, the app also functions excellently as a reference, enabling new operators to soon start working on their own. In doing so, however, Kvadrat Eibergen was in for a surprise, says Kilian. ‘The work instructions are now created by experienced operators, which is the whole point, of course. When we started using these, we soon learned that operators find some things so obvious that they aren’t – or not fully – included in the app. Or that certain experienced operators do things slightly differently. Which is why we are currently adapting a number of the work instructions so that they are explicit and sufficiently clear for beginners.’
Detmar is satisfied with what has already been achieved in six months. ‘We are seeing hygiene, neatness and tidiness improving, because activities have been scheduled, checked off, and because there is certainty as to what a production site should look like. In the beginning, some operators were wondering if this type of digital app was really necessary, but now they are enthusiastic and we are getting more and more requests, such as ‘can this be included too?’ In addition, we also see the action-reporting function being used more and more. Here, for example, an operator might report that a trolley needs to be cleared away. At the moment, all reports are centrally received by a team leader, who then determines to whom the action is assigned.’
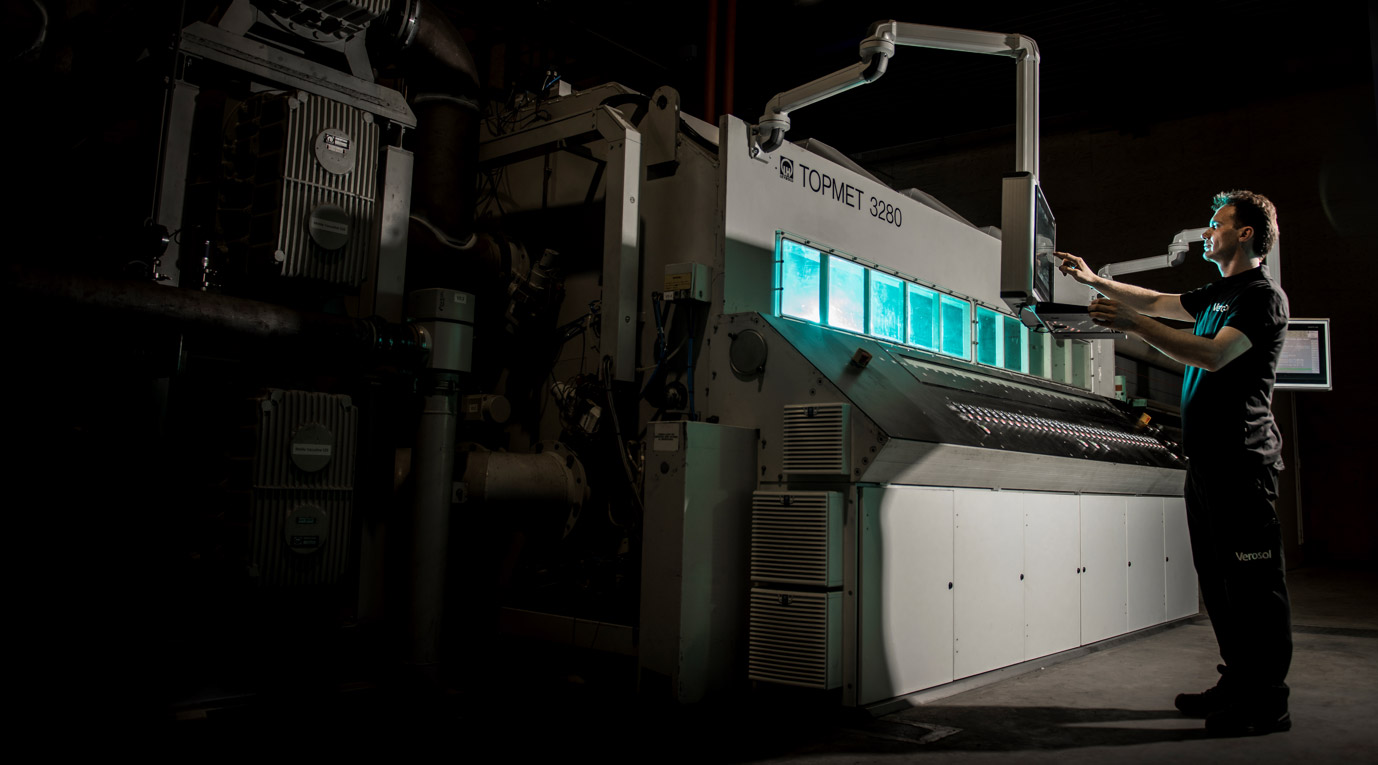
It is no coincidence that Kvadrat is currently undergoing this professionalisation process. The company is moving fast. After long-term ownership in the hands of an investment company, it has been part of a committed Danish parent company since 2019. From July 1 2022, Verosol’s name changed to Kvadrat. ‘We are now really catching up with investing in people and production capacity,’ says Detmar. ‘It is certainly difficult to find people in the current labour market, so thorough education and training is extremely important for us.’
Kvadrat Eibergen currently equips all Booking.com office buildings with solar shades; at the same time, it is engaged in numerous other large projects, and also serves the retail market. Which means you need to get things right. There’s no issue on that front, confirms Detmar. ‘The learning capacity of this system was an important reason for us to opt for EZ-GO. We can measure the safety, quality and speed of processes, and adjust where necessary. If new products and processes emerge, we can easily add them. And everyone can work with them.’